To understand what root cause is, lets first look at how we deal with problems in everyday life. Say at work we suddenly feel unwell. We would probably take some generic medicine such as paracetamol to relieve the symptoms temporarily. If the symptoms continue, we go to the doctor to understand what the reason behind the unwell feeling is. In this simple example, the doctor performs the root cause analysis of the patient by solving the problem at its source.
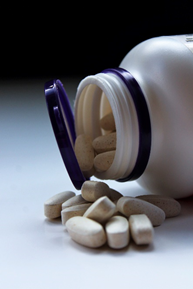
Many times, in both life and business, when faced with a problem, we take the paracetamol approach. Just like feeling sick, it sometimes works just enough that the underlying problem heals on its own or it is ineffective in treating the main cause. The reason for taking this approach is the fact that it is easy to apply, requires less thinking and is a one size fits all solution.
In this article, I will focus on root cause analysis from the perspective of our work life.
The basic assumption that root cause works on is the idea that it is more effective and less expensive to find a long-lasting solution to address the root cause than to keep addressing symptoms and short-term problems.
The three steps to an effective root cause analysis strategy are:
- Identify the root cause.
- Fix the root cause.
- Apply the knowledge from the solution to prevent future issues.
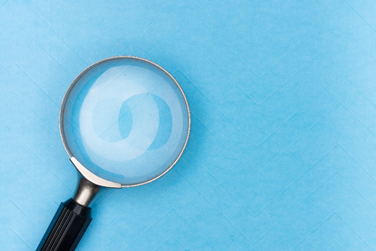
In the identification stage, many people mistake the symptoms for the root cause or assume that they can be only one root cause of a given problem. In the first instance, the solution applied will not be of much use as it is the same case of treating the symptoms instead of the underlying issue. The second case, however, is a fundamental mistake in assumption. It is important to not make the mistake of assuming a one-to-one relation between cause and problem. Many times, a combination of causes creates a problem.
Another thing to keep in mind during identification is to identify the correct cause.
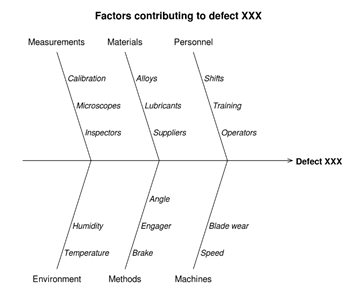
One method developed to correctly identify the various root causes is the Ishikawa diagram (also called the “fishbone diagram”. In this method, a problem is first identified and then all the causes that lead to the problem as identified and put in a forked structure as illustrated in the diagram above. The main benefit of this method is that many causes can be visualized at the same time thereby leading to better categorization of the various causes and the grouping together of similar ones.
Another such method is the concept of “5 Whys”. We first ask the question “Why?” to the problem and obtain an answer. Then we ask “Why?” to the answer we received. This process goes until we have asked “Why?” five times the final answer of which would likely be the root cause.
Do note that these are only two technique among many and the choice to selecting one depends on your personal preference to suit the facts of the case.
The next step is to then find a solution to the underlying problem we have identified. Problems of different nature require different resources to address them. For example, a people issue cannot be dealt with the finance department or money. It would fall on the ones best suited to such fields such as the HR or admin department. Similarly, a machine issue cannot be addressed by the HR department but must be addressed by the engineering team.
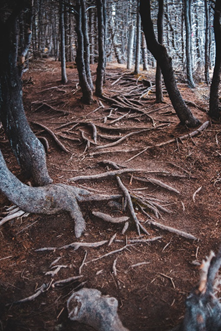
It is particularly important to get this step right. Many a time, despite identifying the root cause, organizations tend to just address the symptoms, and this could be for many reasons such as ease, saving of time or cheaper fix which do provide the mentioned benefits but only for the long term. Hence, in any case, other than urgency, it would be better to fix underlying issues.
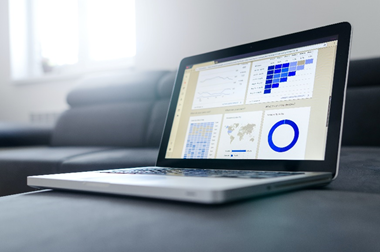
As part of this, it is also important to study the cause-and-effect relationship. Say we decide to implement a solution. It does not end there. We must go back and see if the solution we have implemented is successful in addressing the symptoms because, at the end of the day, the existence of symptoms means there is still something wrong. Maybe we have not addressed all the root causes. Or maybe our solution is just not effective. This is something that rarely occurs but is worth keeping in mind.
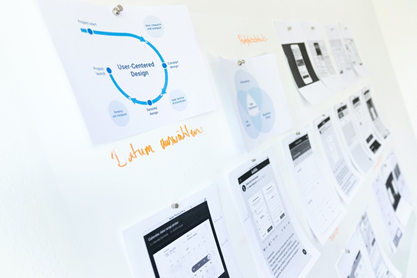
The final step is to implement preventive measures based on our solution or what we learned from this root cause analysis exercise. This is to ensure that the same issue does not happen again. For example, let us look at the following scenario. Say we have an issue where we find the number of units produced has not improved despite using a new machine in the production process. During root cause analysis we find the reason for the same is due to not training the staff on using the new machine effectively. The solution was to train them thereby improving productivity. But then what? Do we stop here just because everything is working fine? The answer is no. We must put in place a system that prevents the same issue from happening again. An example of such a system would to either train employees regularly or at least whenever there have been improvements in technology. I hope this example gives a good idea of the root cause analysis process and application.